For the past few years, 3D printing has been touted as the next big thing in manufacturing. But could this technology — often hyped for its “cool” factor but little more — hold one of the keys to addressing climate change?
Climate change is a massive problem that needs to be tackled on multiple fronts. At polySpectra, we’re making a big bet on a potential solution that involves changing the way the world makes things.
The Poor, Misunderstood Carbon Footprint
In the past two decades, general awareness of climate change and the concept of the “carbon footprint” has risen dramatically. But despite this growing awareness, the full complexity of the carbon footprint paradigm hasn’t made its way into popular consciousness.
A product’s carbon footprint measures the greenhouse gas emissions — commonly reported as carbon dioxide equivalents — at each stage of a product’s life. When we talk about the carbon footprint of a given product, like a gallon of milk, a car, or even a house, we have to take into account a number of different factors — some obvious, and some less so.
Although many consumers are aware of the impact of transportation on the carbon footprint of a product or activity (witness the popularity of carbon offsets for air travel, or Lyft’s announcement to offset all ride emissions), the total carbon footprint for a given product also includes crucial factors such as the materials used to make the product, and the manufacturing processes that turn those materials into end products.
In particular, manufacturing is popularly underappreciated and misunderstood in terms of its contribution to the carbon footprint of new products. But there’s a silver lining to this lack of awareness: advances in manufacturing technology offer huge potential to reduce the carbon footprint of manufactured goods and make a difference in the battle against climate change.
The key to unlocking that potential? That lies with additive manufacturing (AM), also known as 3D printing.
The Emission-Curbing Potential of 3D Printing
The simple fact is that many of the methods available to us for reducing carbon dioxide emissions are hiding in plain sight. While slapping solar panels on your roof will almost certainly have a positive effect on your family’s carbon footprint, that footprint is likely to be much more impacted by less-visible changes to the methods used to make the durable goods you use every day.
Some reports have suggested that the carbon “cost” of manufacturing a new car, for instance, might be greater than the carbon cost of actually driving the car into the ground. If we can lower the carbon cost of manufacturing that car, we can potentially make a bigger difference than we would by attempting to maximize miles per gallon over the life of the vehicle.
Perhaps no technology offers greater potential to reduce the carbon footprint of manufactured products than additive manufacturing.
Additive manufacturing describes the process of building 3D objects using layers of material. Known popularly as 3D printing, additive manufacturing began back in the 1980s with the commercialization of stereolithography, a process that uses a laser to solidify thin layers of ultraviolet (UV) light-sensitive liquid polymer.
This technology, which has been around for several decades but is still undergoing rapid improvements, could help lead the way to a carbon-lighter future.
A recent paper from researchers at Delft University of Technology predicts that additive manufacturing could reduce global energy usage by 25% by 2050. That is a massive impact! Even extremely aggressive scenarios for deploying renewable energy at enormous scale would have a hard time hitting that kind of impact on emissions. In order to understand why 3D printing provides such a huge lever on global energy usage, we need to dig into the details of how stuff is made.
How 3D Printing Can Improve the Carbon Impact of Manufacturing
Additive manufacturing offers the possibility of creating high-performance materials and processes with smaller carbon footprints — and it promises to do so by addressing the carbon impact of the three major facets of a product’s carbon footprint: materials, manufacturing, and transportation.
A quick note before we dive in. For the sake of simplicity, I’m going to use carbon footprint and energy interchangeably below. For some of these contributing factors, energy and carbon dioxide emissions can be decoupled (for example, by running the manufacturing tools on solar electricity), but for others (like extracting raw materials out of the earth and processing them into well-defined molecules) they are so intertwined that energy and carbon footprint cannot be separated.
Here’s how 3D printing could help radically reduce the carbon footprint of manufactured items.
1. Materials (Embodied Energy)
The embodied energy within the materials that products are made out of is an important yet almost invisible contributor to the total carbon footprint of a product. Because the synthesis and processing of materials such as plastics and metals is so far removed from our everyday experience as consumers, it’s easy to forget about it. It’s also pretty difficult to change the embodied energy of a material without changing its production process and final properties. For now, let’s think of the embodied energy as everything that goes into the extraction, purification, production, and transportation of raw materials.
One key way that 3D printing can reduce the materials component of the carbon footprint is by enabling energy-efficient geometries that use much less material than traditional manufacturing processes. This is known in the industry as dematerialization. Reduced materials waste is another potential benefit, assuming that the 3D printing process is efficient.
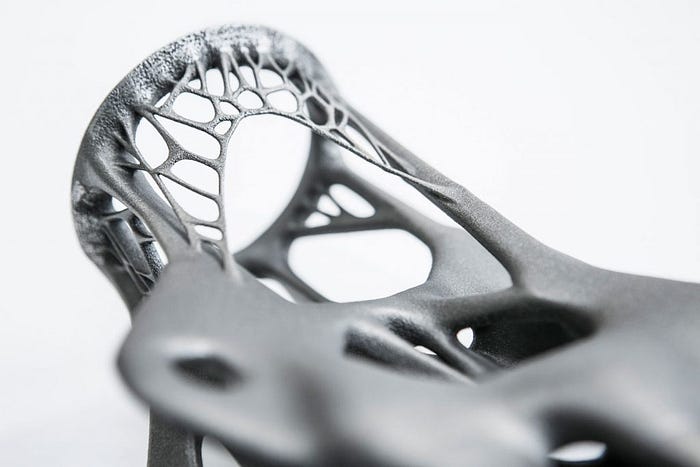
A generatively designed light-weighting structure, demonstrating the ability of additive manufacturing to dematerialize the final component. (Same performance with less mass.) Image via Autodesk.
Another way in which 3D printing can reduce a material’s embodied energy is by displacing parts that would have traditionally been made with a high-embodied-energy material. For example, not every metal part in a vehicle or piece of equipment really needs to be made out of metal. In many cases, 3D-printed polymer or composite parts can do the job just as well, offering a lower embodied energy (and often lighter-weight) solution.
2. Manufacturing (Process Energy)
The process energy accounts for everything involved in forming the raw materials into the usable end product, including manufacturing, assembly, and packaging. Like the embodied energy of the starting materials, this is usually out of sight and mind for most consumers. Unless you are an engineer or a die-hard fan of How It’s Made, manufacturing processes are not likely top of mind while you’re shopping on Amazon.
When it comes to 3D printing, there are many classes of 3D printers, many of which are incredibly energy intensive to run. Process energy is not necessarily a category in which additive manufacturing is guaranteed to win, but there are specific cases where 3D printing uses way less energy than a traditional manufacturing process. Let’s take an example close to polySpectra’s heart: comparing the energy usage of a typical benchtop-sized DLP printer (based on the stereolithography process mentioned above, except using a projector instead of a laser to cure the material) and a traditional injection molding tool. The difference in the process energy is 100X. Yes, that’s right: DLP printing processes can use as little as 1% of the energy of an injection molding tool.
3. Transportation
This involves the transport, storage, and handling of the product to the end user. Perhaps the biggest impact of 3D printing on the transportation component of carbon footprint is that it will make it largely obsolete! With the ability to produce parts on demand, zero-inventory manufacturing becomes possible. Any 3D printer location can become its own “virtual warehouse” of products that can be produced on location as needed.
If you want to get a good sense of the massive carbon footprint of our current global shipping and logistics infrastructure, just watch this video on how overnight shipping works. If you know anything about the carbon footprint of flying, you should be terrified:
3D printing offers the possibility to make what you need, where you need it, in the quantities you need. Distributed digital manufacturing means shorter lead times as well as lower transportation energy. This doesn’t necessarily mean “a printer in every home,” but instead a decentralized network of additive manufacturing nodes capable of addressing regional demand.
As a bonus, the ability to create products with more energy-efficient geometries that use less material also means that when products do need to be shipped, their much lighter weight incurs a much lower carbon cost by improving the fuel economy of the cars, trucks, airplanes, and other vehicles used to transport those products.
If you’re still trying to figure out how additive manufacturing could possibly reduce global emissions by 25%, transportation is definitely the longest lever. About 30% of the US energy usage in 2017 was for transporting goods and people from one place to another! 3D printing enables the virtual warehouse, which will eliminate a huge portion of the footprint of transporting goods. It also unlocks light-weighting and dematerialization engineering strategies for vehicles that will dramatically lower the energy required to transport people.
Where polySpectra Comes In
polySpectra is working on creating materials and 3D printing processes that will use less energy, produce fewer emissions, and ultimately help mitigate the progression of climate change. Our mission and mandate is ambitious: to create high-performance AM materials and processes with overall carbon footprints that are a fraction of today’s state-of-the-art materials and processes.
The catch for all of the comparisons above is this: in order to have a chance of making an impact, you first need 3D-printed materials with the performance and durability to displace traditional manufacturing processes. Despite the never-ending hype around 3D printing, examples of printed parts being employed to directly additively manufacture durable goods are few and far between. Therefore, the first part of our mission is to commercialize the most rugged 3D-printed polymers on the market, capable of going head-to-head with injection-molded engineering plastics.
As a fun example, we’ve put together a small table to show the dramatic reduction in estimated carbon dioxide equivalents of printing with our COR Alpha material, compared to injection molding with three common engineering plastics.
Estimated carbon footprint comparing 3D printed COR Alpha to three common injection molding polymers.
In sum, COR Alpha could enable the direct 3D printing of engineering-grade polymer products capable of displacing traditional manufacturing methods. With COR Alpha, we can 3D print parts with the strength, toughness, and working temperatures of today’s state-of-the-art polymers — with the bonus of a significantly reduced carbon footprint.
If we’re successful at using polymers like COR Alpha to dramatically lower the energy required to manufacture durable goods, we’ll unlock a new paradigm of energy-efficient manufacturing by leveraging chemical bonds to displace the work currently performed by electrons. This could have a huge effect on the energy requirements and carbon footprint of manufacturing — and could be a climate change difference maker.
How much of a difference?
The polymers industry employs ~8% of the U.S. manufacturing workforce and consumes ~6% of all the energy used by U.S. industries. If widely adopted, our technology could directly reduce the annual energy usage of the United States by approximately one quadrillion BTU, the CO2 emissions equivalent of removing 44 million passenger vehicles from the road. (Check out this cool calculator from the EPA.) This calculation is just for the manufacturing and embodied energy, it doesn’t even include the potential impact on transportation & logistics, which is even bigger!
And we haven’t been going it alone. polySpectra’s mission to apply cutting-edge chemistry to impact climate change was forged during a fellowship at Cyclotron Road, with the financial support of the US Department of Energy’s EERE Advanced Manufacturing Office and the National Science Foundation. One of our investors, Prelude Ventures, has a strict filter on investing only in companies that can impact climate change. Believe it or not, additive manufacturing companies now represent a significant part of their portfolio.
If you’re as excited about the possibilities for reducing the global carbon footprint of manufacturing with 3D printing as we are, we would love to hear from you. Reply with your comments below, subscribe to our newsletter The polySpectra Pulse, or check out our website to learn more.