What is digital light processing in 3D printing?
When it comes to 3D printing, there are a range of processes available. Digital light processing (DLP) in 3D printing is a process that uses light to harden photopolymer resin. Like all 3D printing processes, there are pros and cons. This article provides an overview of how DLP works in 3D printing.
How does digital light processing (DLP) work?
Digital light processing in 3D printing uses a special type of resin—a photopolymer—that hardens when exposed to light. It works by dividing the structure of the printed part into layers. Each layer is exposed to a specific pattern of light which corresponds to your part’s structure.
What is a photopolymer?
A photopolymer is a type of plastic resin which hardens when exposed to light. When using digital light processing, each layer of photopolymer resin is exposed to a pattern of light, thus hardening the resin layer-by-layer to build the part.
As your 3D printer runs through your part’s layers, the leftover resin (which isn’t hit by light) remains a liquid which easily separates from the hardened area. This reduces excess waste material during production of your part.
How DLP uses patterns of light in 3D printing
In DLP, each layer is represented by a single flat image which corresponds to a top-down voxel view of the layer. The light projected onto the photopolymer resin follows this voxel pattern for each layer. An older additive manufacturing technology—stereolithography (SLA)—works similarly by moving a single laser point across the surface of the resin layer.
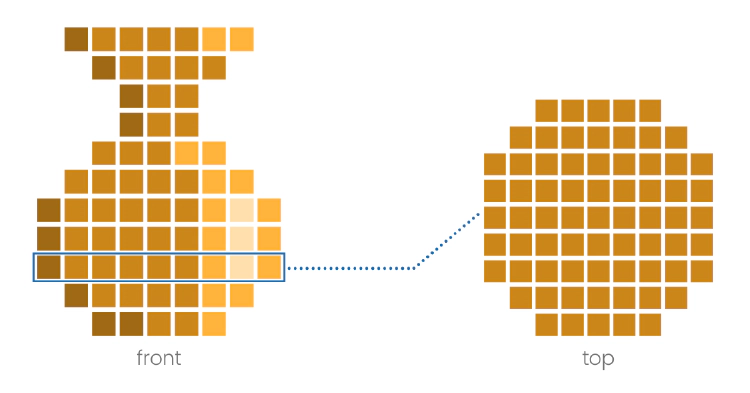
A voxel pattern is created for each layer of the 3D printed design.
A voxel is a volume element, defined in 3D space. Think of voxels like 3D pixels: the higher the resolution, the smoother (and more scaleable) your part can be. But if you’re worried your part will look pixelated, don’t be—most resin 3D printers can produce a resolution of between 25 and 75 microns!
Practical applications of 3D printing with DLP
Digital light processing is a fairly new technology, but it’s tried and true across several industries. A great example is 3D printed electrical connectors. Estimated at $70B/year, the electrical connector market is a huge component of several industries including automotive, aerospace, and computational tech. Additive manufacturing meets the demand of introducing design variations across thousands of connectors produced on a daily basis.
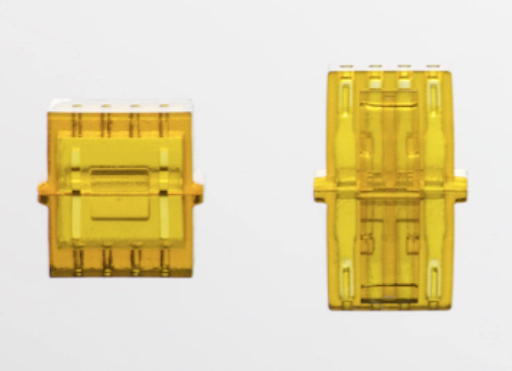
3D Printed Electrical Connectors.
A production-grade connector must be able to withstand heavy use and harsh environments. COR Alpha connectors can meet the specifications required for weather-proof and long-term, reliable use of electrical connectors.
→ Read more: Application Highlight: Electrical Connectors
Another practical application for digital light processing in 3D printing is for complex structures, such as latticework. Latticework is not easily produced via traditional manufacturing processes such as injection molding. As such, up until recently (with the invention of 3D printing in manufacturing) latticework was all but unseen in mass produced plastics.
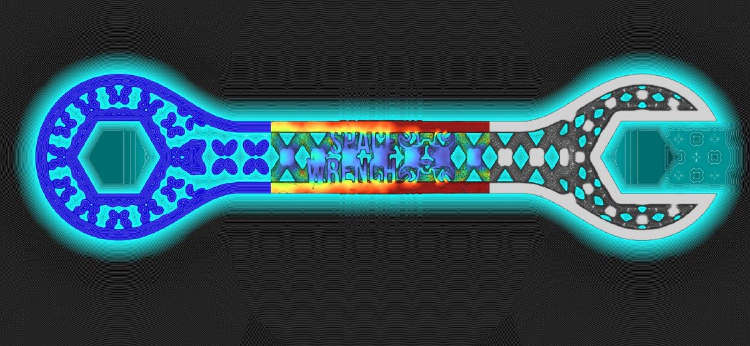
Lattice saves on weight and material. polySpectra’s lightweight _SpaceWrench has a lattice structured interior, competing in strength with solid wrenches
Digital light processing is remarkable for creating complex structures because it lacks issues associated with areas of one layer cooling too quickly for proper adhesion to the next. In comparison, stereolithography does not bode well due to the logistics of moving a single point across each complex layer of a lattice. A printed part with a latticework structure can be just as strong while weighing much less than its solid counterpart. Additionally, this type of structure uses much less material to produce than traditional solid parts.
Digital Light Processing: Pros and Cons
What are some of the specific advantages and disadvantages of using DLP in 3D printing? Like all manufacturing processes, there are some things to consider.
Pros
DLP Printers are capable of printing parts with the accuracy and surface finish rivaling traditional polymer manufacturing processes such as injection molding
DLP is much faster than SLA, which uses a single laser point to harden a layer. This reduces issues with z-strength associated with parts of one layer cooling too quickly for proper adhesion.
It is easier to make complex structures, such as latticework, with DLP.
Cons
DLP uses photopolymers. Many of the photopolymers have poor thermomechanical properties resulting in brittle and fragile printed parts. While this narrows your material options, we designed COR Alpha to resolve this specific issue.
DLP printing requires very precise digital and optical modeling, while also accounting for chemical and material details in the print process. Design for additive manufacturing (DfAM) is an emerging discipline—so there aren’t a lot of expert designers out there. Book a consultation with one now!
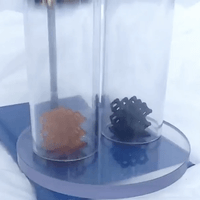
polySpectra’s COR Alpha (left) vs. an “engineering grade” photopolymer (right)
Closing thoughts
Digital light processing (DLP) is an emerging process in 3D printing. To print using this method, a digital 3D model is sliced into layers. In process, each layer has a unique voxel pattern which is projected as light onto a film of photopolymer resin. DLP is less prone to issues with z-strength than stereolithography (SLA) because DLP moves more quickly than layers typically cool. There are many practical applications for this type of additive manufacturing, including connectors and latticework. DLP is an accurate and versatile 3D printing process. It requires a specific type of resin, as well as very precise digital and optical modeling.
Ready to get started with DLP?
Go beyond prototyping: our best-in-class photopolymer material, COR Alpha, is optimized for true engineering-grade additive manufacturing. COR Alpha won’t break or shatter during regular use, and because of how DLP works, you can expect production-grade parts. Start by uploading your digital model. Our team of engineers and materials specialists are experts in digital light processing for 3D printing. We will discuss your specific design needs and provide a free cost estimate.